|
Напыление, плазматрон, плазменное напыление, установка плазменного напыления, газопламенное напыление, металлизация, металлизатор, газотермическое напыление, плазменные покрытия, дозатор порошковых материалов, плазмотрон ПП-25, источник питания ИПН 160/600, УПУ-3Д, комплекс плазменного напыления, напыление керамических покрытий, газопламенная горелка Castodyn-8000, термоэлектрический генератор, керамическое покрытие, жаростойкое покрытие, износостойкое покрытие, ремонт ГПА, горелка для наплавки, дробеструйная обработка, дробеструйная камера, пескоструйная обработка, дробеструйный пистолет, механическая обработка газотермических покрытий, мобильная шлифовальная головка, контроль качества газотермических покрытий, переносной твердомер ЭЛИТ-2Д.
г. Екатеринбург тел: 8-902-87-601-91, 8 (343) 348-75-21
e-mail: 120167@bk.ru
plasma.y1.ru
Распечатать
Загрузить текст в Word-формате (18.9 Mb)
|
- Плазменный метод нанесения покрытий
- Газопламенный метод нанесения покрытий
- Дробеструйная обработка
- Механическая обработка газотермических покрытий
- Контроль качества газотермических покрытий
|
5. Контроль качества газотермических покрытий
5.1. Входной контроль предусматривает:
- наличие и проверка сопроводительной документации (технологическая карта) на восстанавливаемую поверхность детали с указанием места напыления, ширины и толщины покрытия, твёрдости напыляемого слоя, геометрии занижения размеров под напыление и т.д;
- внешний осмотр восстанавливаемой (напыляемой) поверхности: определение характера и величины износа, осмотр повреждений поверхности с целью выявления недопустимых дефектов (раковины, царапины, сколы, трещины, коррозия).
- контроль поступающих и расходуемых материалов: дробь чугунная колотая, корунд, порошки для напыления, средства для обезжиривания, ветошь и т.д.
5.2. Технологический контроль предусматривает:
строгое соблюдение всех рекомендаций и указаний технологической и технической документации в процессе подготовки и нанесения покрытия на поверхность детали и последующей механической обработки восстановленной поверхности.
5.3. Окончательный (выходной) контроль предусматривает:
оценку качества покрытия после механической обработки:
- произвести внешний осмотр покрытия невооружённым глазом с целью выявления наличия пор, трещин и отслоений. Поры, отслоения и трещины, видимые невооружённым глазом в покрытии не допускаются;
- произвести измерение твёрдости покрытия не менее чем в трёх точках на восстановленной поверхности. Если деталь имеет цилиндрическую форму, то оценку твердости необходимо произвести в трех точках в каждом из трех поперечных сечениях. Среднюю величину полученных значений считать фактическим значением твёрдости покрытия. Измерение твёрдости производить на реальных деталях или на образцах свидетелях стандартным способом путём вдавливания тела (индентор), выполненного в виде стального шарика, алмазного конуса, пирамиды или иглы. По размерам полученного на поверхности покрытия отпечатка судят о твёрдости материала покрытия. Для измерения твердости покрытий нанесенных на поверхность крупногабаритных деталей рекомендуется использовать переносной твердомер ударного типа марки ЭЛИТ-2Д (Рис.23). Данный прибор позволяет производить измерение в пределах двух шкал твердости: HRc и HВ. Вследствие наличия незначительной пористости в напыленных покрытиях использование для измерения твёрдости приборов основанных на ультразвуковом методе оценки недопустимо.
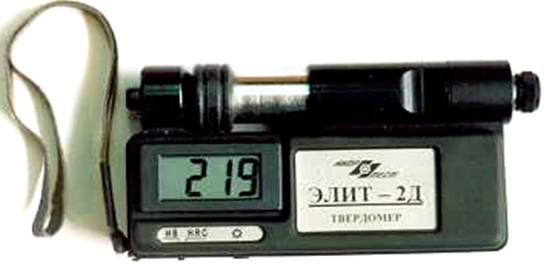
Рис.23. Твердомер Элит-2Д.
|